1. What is free radical polymerization?
Free radical polymerization is a widely used method for creating polymers from vinyl monomers. free radical polymerization proceeds through a chain reaction mechanism consisting of initiation, propagation, chain transfer, and termination as the elementary steps. Azo compounds and peroxides are the main commercially used initiators used in free radial polymerization processes.
1-1. Reaction mechanism of radical polymerization (elementary reactions)
The first reaction, or initiation reaction generates highly active free radicals that react with monomers to generate propagating radicals. Next, in the propagation reaction, these propagating radicals continue to react with the available monomers resulting in the efficient formation of polymers. The termination reaction occurs when the propagating radical polymer undergoes recombination or disproportionation. Chain-transfer reactions occur when the propagating radical reacts with another chemicals species in the system.
1-1-1. Initiation reaction
The most general method for radical generation is the thermal decomposition of peroxides or azo compounds. Active monomeric free radical species are generated as a result of the free radicals created by the decomposition of the initiator, this is called the initiation reaction.
Active monomeric free radical species are generated as a result of the free radicals created by the decomposition of the initiator, this is called the initiation reaction.
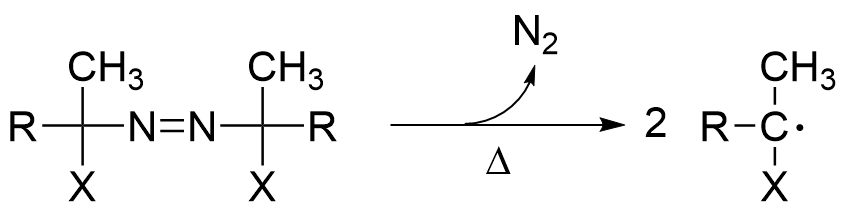
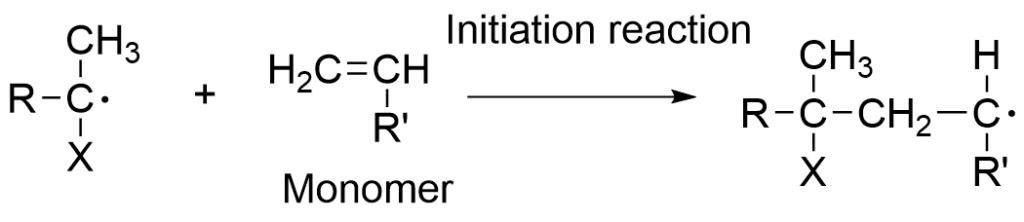
Our company offers azo polymerization initiators with various structures, including those that are soluble in organic solvents and those that are soluble in water. Please use them according to your application.
Check the types of azo polymerization initiators and how to select one
Here, you can calculate the ‘residue rate’, ‘decomposition reaction time’, and ‘temperature during the decomposition reaction’ of azo polymerization initiators.
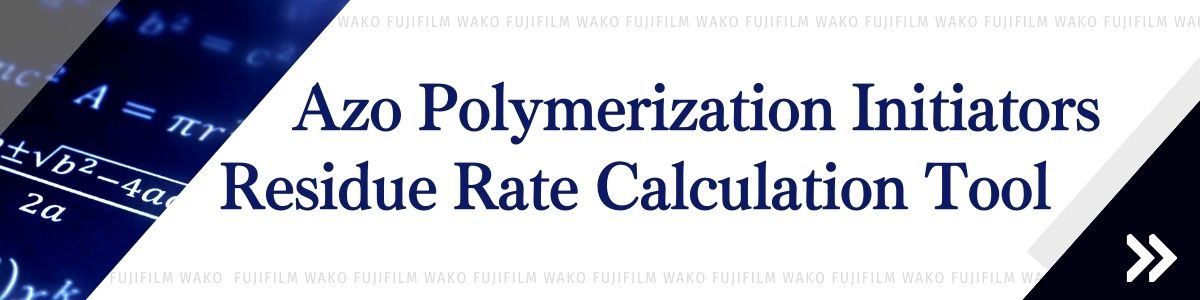
1-1-2. Growth reaction
The propagation reaction is characterized by rapid and simultaneous reactions between the radicalized monomer and other monomer molecules to extend the polymer chain. The radical that functions as an intermediate in the propagation step is called the propagating radical.
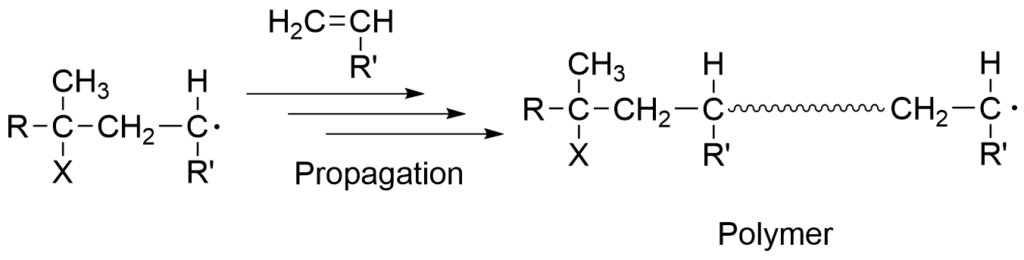
1-1-3. Termination reaction
In this step the propagating radicals become inactivated. The most common termination reaction is recombination, where two radicals recombine with each other. Another type of termination reaction is called disproportionation, where a hydrogen atom is transferred from one chain to another resulting in one saturated and one unsaturated chain.
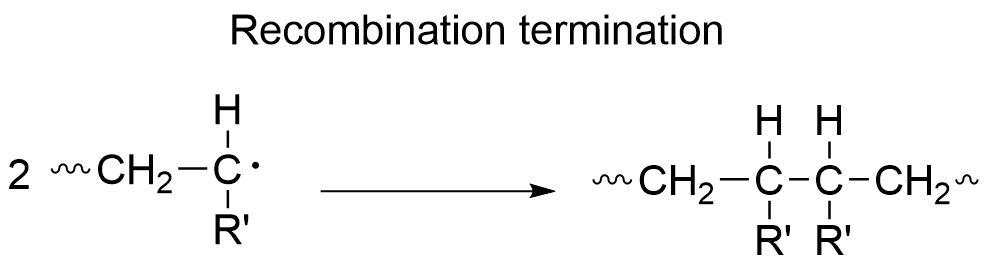
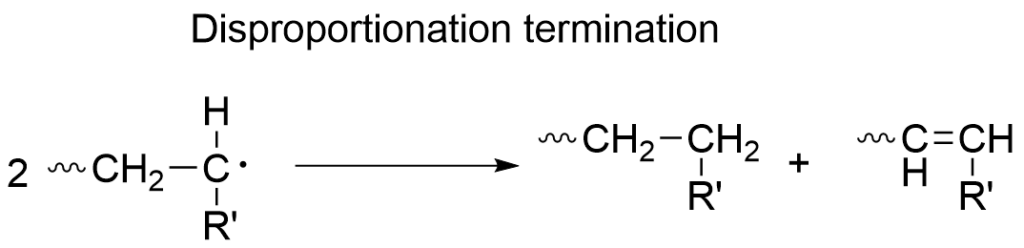
These termination reactions affect the molecular weight distribution in free radical polymerizations, and a polymerization technique that controls the molecular weight distribution is called the living radical polymerization.
In addition, polymerization inhibitors inhibit the monomers from readily reacting with radicals.
High-performance polymerization inhibitors Q-1300 and Q-1301 of our company deliver powerful polymerization inhibition effect during purification and storage of highly reactive monomers.
Check the details on high-performance polymerization inhibitors, including their mechanism
1-1-4. Chain transfer reaction
Chain transfer reaction is explained in detail in the section for living radical polymerization.
1-2. Characteristics of radical polymerization
Characteristics of radical polymerization are listed below.
Free radical polymerization is widely used in industrial applications thanks to the following characteristics
- Various types of monomers can be used (materials of various physical properties can be synthesized).
- It does not require as many specialized facilities as other methods.
- Relatively mild reaction conditions are required for operations.
- The process is not inhibited by humidity.
Special caution is required on the following at the time of implementation.
- Oxygen inhibits the reaction.
- Reaction is highly exothermic, resulting in some risk of runaway reaction.
1-2-1. Differences between radical polymerization and ionic polymerization (cationic polymerization or anionic polymerization) (comparison)
In free radical polymerization, the activated species does not react with water or ionic substances in principle but rapidly reacts with double bonds. Therefore, it is not necessary to remove impurities such as polar substances, and polymerization can be conducted in water. Ionic polymerization differs from radical polymerization significantly. Only certain vinyl monomers may be used due to the reaction’s incompatibility with water and polar groups, in general. Electronic forces of the growing species also greatly affect the polymerization reactivity.
On the surface, it appears as if the only differences between radical polymerization and ionic polymerization (cationic and anionic polymerization) are the initiator and activated species.
However, when a co-polymer of styrene and methyl methacrylate is synthesized, anionic polymerization using n-butyllithium forms a co-polymer rich in methyl methacrylate in any of the compositions, while radical polymerization using benzoyl peroxide (BPO) delivers a co-polymer with a composition nearly equivalent to that of the monomer. In cationic polymerization using tin tetrachloride as the initiator, polymerization of styrene occurs predominantly.
As you can see, the reactivity of the monomer varies depending on the type of chain that is grown.
Furthermore, the reactivity varies greatly depending on the activated species, and
Reaction time: Radical polymerization (approx. 1 hour) > Anionic polymerization (approx. 1 minute) > Cationic polymerization (approx. 1 second) is often used as typical estimated values.
1-3. Types of radical polymerization (available azo initiators)
1-3-1. Bulk polymerization
Bulk polymerization is a type of polymerization that is conducted by using only monomers or by adding a small amount of polymerization initiator without solvents.
Select an initiator that dissolves in monomer.
1-3-2. Solution polymerization
Solution polymerization is a method of polymerization that is conducted in a solvent. The solvent used for solution polymerization is one that does not readily to react with either the monomer or the initiator.
Select an initiator that dissolves in monomer and solvent.
1-3-3. Emulsion polymerization
Emulsion polymerization is a method of polymerization that uses water as the medium to prepare an emulsion of the monomer in the presence of a surfactant (emulsifier), and that is conducted by adding a water-soluble polymerization initiator to it.
Emulsion in which the polymer particles are dispersed in the medium such as water (also called latex) is formed by this emulsion polymerization. Emulsion polymerization is similar to suspension polymerization, which is described in the next section, but in general, it uses a water-soluble polymerization initiator to generate radicals in water, and therefore the polymerization behavior varies.
Select an initiator that dissolves in water but not in monomer.
1-3-4. Suspension polymerization
Suspension polymerization is a method of polymerization in in which the monomer is suspended in water by mechanical agitation (stirring) before and during polymerization. The polymer is obtained in small spheres (pearl-shaped).
It is also called bead polymerization, granular polymerization, and pearl polymerization.
Select an initiator that dissolves in monomer but not in water.
2. Typical examples of radical polymerization
Reaction formulae of typical examples of radical polymerization are shown below.
2-1. Radical polymerization using styrene (reaction mechanism)

2-2. Radical polymerization using acrylic acid ester (reaction mechanism)

2-3. Copolymerization of styrene and acrylic acid ester (reaction mechanism)

3. What is living polymerization?
Living polymerization is a method of polymerization that is effective in synthesizing polymers whose structures are precisely controlled, and it is defined as “chain propagation polymerization consisting only of initiation and growth, which does not have irreversible termination or transfer.”
Living polymerization was first reported in 1956 by Michael Szwarc with anionic polymerization of styrene, and the concept of living polymerization was also proposed in this report.
Subsequently in the 1980s to 1990s, living polymerization was further developed for chain propagation polymerization of various mechanisms, and it became possible to conduct living polymerization of polymers with a structures that were previously unavailable to polymer scientists (such as polymers built with highly polar monomers). In the 1990s, living polymerization was developed for radical polymerization, which was previously considered impossible. This process is based on stable radicals, transition metal complexes, or reversible chain transfer. At present, living polymerization has been developed with various mechanisms, including anionic, cationic, radical, coordination and ring-opening (ionic, metathesis).
These methods of synthesis are called precision polymer synthesis, and the polymers synthesized are often called precision polymers.
3-1. What is living radical polymerization?
Due to the large size of its application scope, living radical polymerization has become an essential means for obtaining high-performance materials required in various areas, such as electronics and medical materials, in addition to polymer industries.
Conventional radical polymerization has characteristics that make it difficult to precisely control the molecular weight. It is difficult to control the occurrence of the termination reactions caused by recombination and chain-transfer as described above.
On the other hand, living radical polymerization, which reversibly generates the radical species, allows the propagating radical species to be temporarily converted to the inactive dormant species and suspend the growth of the polymer chains. When the exchange reaction between the dormant species and radical species occurs rapidly, all of the polymer chains in the reaction system undergo the growth reaction at the same rate, resulting in formation of polymers with the uniform molecular weight. Furthermore, since the dormant species and the radical species are in equilibrium, it is possible to lower the concentration of the radical species by moving the equilibrium toward the dormant side and thus suppress the side reactions.

3-1-1. Living radical polymerization that progresses with reversible chain transfer (RAFT polymerization) mechanism
Polymerization progresses with a reversible chain transfer where the terminal polymerization radical is added to the carbon-sulfur double bond of the thioester and new activated radical and dormant species are formed by way of intermediate radicals. This mechanism is called the Reversible Addition-Fragmentation chain Transfer (RAFT) polymerization.
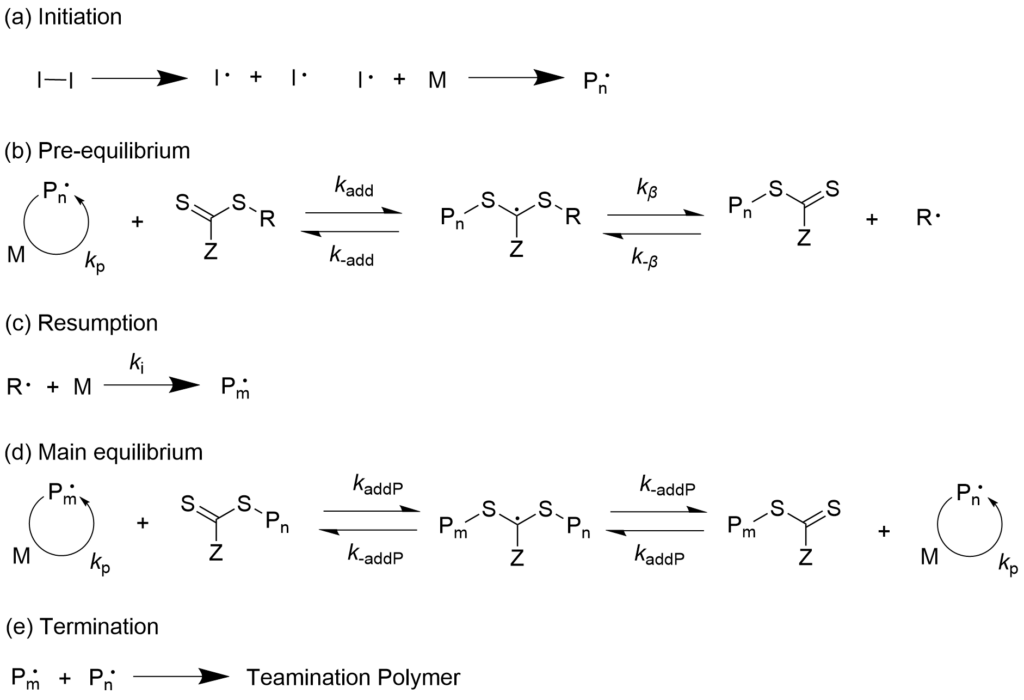
With combination of our company’s azo initiators and RAFT agents, precise polymerization reaction becomes possible by only adding them to the existing polymerization system. Our company has a lineup of many RAFT agents that can be provided for mass production level. We also accept contract manufacturing of RAFT agents.
3-1-2. Nitroxide-mediated living radical polymerization (NMP) mechanism
Nitroxide-Mediated radical Polymerization (NMP) was first reported as radical polymerization of styrene using 2,2,6,6-tetramethylpiperidine-1-oxyl (TEMPO), which is a representative stable nitroxide radical. In this case, it was shown that polymers with a molecular weight of several tens of thousands and a relatively narrow molecular weight distribution (Mw/Mn < 1.3) could be obtained by polymerization under the conditions where TEMPO was added to the radical polymerization system for styrene with benzoyl peroxide as the initiator. Thanks to the molecular design of nitroxides, it has now become possible to apply this to a wide range of monomers, which mainly consist of acrylic acid esters. Because the alkoxyamine compound, which is a dormant species, is stable and can be isolated, it has been widely used in studies of precision polymerization as a “monomolecular initiator” for living radical polymerization.

3-1-3. Living radical polymerization using metal catalysts (ATRP/OMPR) mechanism
Living radical polymerization that combines a transition metal catalyst which undergoes one-electron oxidation-reduction with radical polymerization is roughly classified into two types. One is called Atom Transfer Radical Polymerization (ATRP), and it has a mechanism in which the propagating terminal is capped with a dissociable group such as halogen, which moves between the propagating terminal radical and the metal through one-electron oxidation-reduction of the metal complex (Mn <-> Mn+1). The other is called Organometallic-Mediated Radical Polymerization (OMRP), where the metal is added directly to the propagating terminal as a dissociable group, and one-electron oxidation-reduction of the metal causes the formation of propagating radical species. While the presence of metal residue in the polymer that is formed may be a problem depending on the application, systems where polymerization can be controlled even with a very small amount of metal catalyst have been developed recently. Polymer synthesis methods that do not use metals are preferred for applications such as electronic materials and biomedicine. In recent years, there have also been reports of metal-free atom transfer radical polymerization (O-ATRP) with organic photocatalysts.
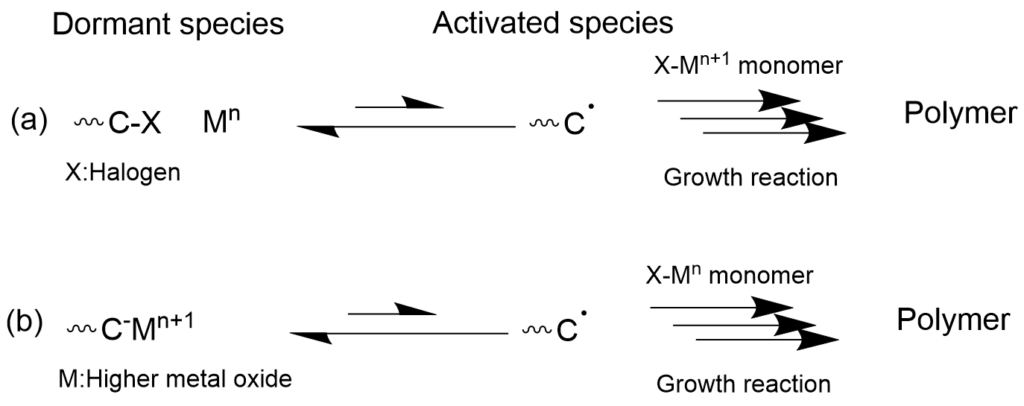
(b) organometallic-mediated radical polymerization (OMRP)