Customer case studies
Example 4:Customer D (foreign pharmaceutical manufacturer)
Product:Intermediate
Succeed in reducing 55% of the cost by introducing our original synthetic method for pyridine derivative
Foreign customer D (pharmaceutical manufacturer) considered reducing the cost for an API they were developing. Therefore, they focused on our synthetic method of 2-pyridine derivative as a manufacturing method of this intermediate.
Cross-coupling reactions, Ullmann reactions or Suzuki-Miyaura coupling reactions are generally used for synthesizing 2-pyridine derivatives. However, these synthetic methods require expensive metal catalysts or reagents, and final product cost is high due to metal removal.
・Expensive metal catalyst or reagent is required for constructing 2-pyridine skeleton.
・Metal removal process is required.
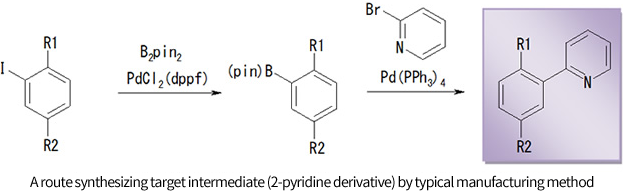
We proposed a novel synthetic route which is effective, safe and environmentally friendly.
We possess the synthetic technique of 2-pyridine derivative by cyclizing the C3 unit (1,3-dimethyl-2-oxopyridinium salt) which was originally developed and acetophenones without using expensive metal catalyst. In addition, we can produce 2-pyridylepyridine by using acetylpyridines instead of acetophenones.
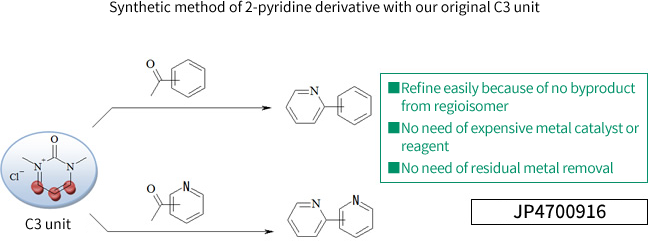
We thoroughly examined with company D whether the synthetic technique above could be applied for constructing a 2-pyridine skeleton while manufacturing the pharmaceutical intermediate. We had a good prospect on cost savings because the synthetic technique did not require metal catalyst and residual metal removal process was omitted. In addition, our organic synthesis research laboratory helped design the fundamental synthetic route. Our production engineering department developed the process for scaling-up. Therefore, we succeeded in shortening the term from method development to delivery of product by fostering cooperation between the laboratory and the production departments from an early stage.
Examination process
- We examined the original synthetic method of 2-pyridine derivative which did not require expensive metal catalyst or reagent. We selected a reasonable route while considering the stability of functional group and the raw material cost.
- We established the manufacturing process with shorter delivery date by integrating the project management system of the synthetic technique department and the production engineering department.
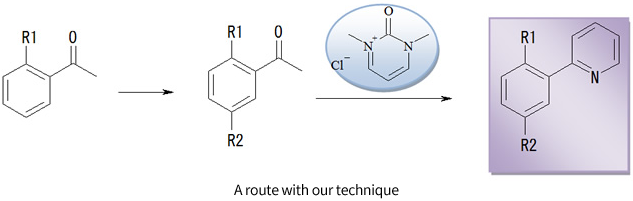
Result
We could contribute to cost reduction of API manufacturing by achieving reducing 55 % of the cost compared to the general manufacturing method with our proposal route. In addition, we succeeded in establishing a manufacturing method that does not impair product quality and is environmentally friendly, owing to no use of metal catalyst and of the absence of residual metal.
Our custom manufacturing /synthesis makes a difference
We have experienced in researching on productization of various raw materials for high-performance materials such as APIs/intermediates, ink dyes, electronic materials, photographs, printing plates and films with a wide range of businesses of FUJIFILM group. The databased abundant performances of crystallization examination obtained through the experiments enable us to search the optimum condition effectively.
Solutions for business issues of company D
- Contributed to customer’s cost reduction by achieving reducing 55 % of the cost.
- Succeeded in establishing the manufacturing method that does not impair product quality (also environmentally friendly) by avoiding the use of metal catalyst.
Please contact us about cost/case/technology/quality control
Inquiry form