GMP compliant manufacturing facility
Hirono plant is a multipurpose manufacturing facility for highly potent APIs. The plant is compliant with category 5 containment and is capable of performing integrated manufacturing techniques including micronization.
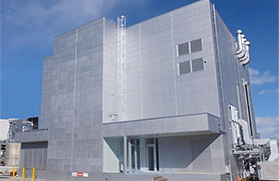
Appearance of 3rd plant
itemProduct |
Equipment specificationsAPI & early phase drugs |
RemarkscGMP non-sterile |
---|---|---|
Facilities |
Containment Area 600 L(GL) Reactor x2 800L Glass Lined Reactor Filter Dryer (0.38m2) Material: Hastelloy C22 equivalent Micronization equipment: Spiral jet mill |
Multipurpose line Minimum mixing volume 50L Minimum mixing volume 50L Dryer filter capacity: 100L Micronization equipment Made by Food and Pharma Systems |
General production area 600L(GL)x1 |
Analytical laboratory management system isolated from production facilities |
|
Containment level | Category 5 | Down to OEL: 0.1μg/m3 |
Cleanliness level |
ISO class 8 c l ean room (Class 100,000 equivalent) |
|
Temperature range | -15~100℃ | Reactor Jacket media: Brine |
Building dimension |
Approx. 900m2 2 floor s teel ACL concrete |
Milling and crushing of APIs
Various types of mills and crushers are available to meet API manufacturing requirements.
Counter jet mill
・Particle diameter 5 μm or less
Hammer mill
・Particle diameter 5 μm to 50 μm
Power mill
・Various types of screens are available.
・Round hole screen: 2 mm, 3 mm, and 5 mm
・Herringbone screen: 2 mm
Highly versatile spiral jet mill
- Milling particle diameter: 1 μm to 30 μm
- Production quantity: up to 30 kg/hr. 100 g to 100 kg/batch
- Simple structure that allows for easy cleaning Cleaning is possible in the isolator.
- Large particle sizes (up to 100 μm) are also possible. e.g. Q-MILL: up to 100 μm
- Can be expanded to handle milling at an extremely low temperature (-90°C)
- Prior testing of the milling capability can be performed(200 mg/batch)
Particle diameters can be controlled by adjusting the feed pressure, milling pressure, and feed amount.
※ Cited from FPS milling machine catalog of CORRENS CORPORATION
Custom manufacturing facilities for pharmaceutical products
Various kinds of facilities and equipment can cover a wide range of scale.
We propose the process with the optimal facility according to the stage from development to commercial production.
Facility |
Scale |
QMS |
Special notes |
---|---|---|---|
Pilot production manufacturing | Capable of Scale-up checking (Hiratsuka plant) | ||
40~100L (GL) | nonGMP | Kilo lab facility | |
600~1,500L (GL) | nonGMP | 600L fluoride resin lined reactor | |
API, Clinical trial API manufacturing | Capable of small-scale manufacturing (Miyazaki plant) | ||
1~20L(GL) 200~500L(GL/SUS/HAS) |
GMP | ISO class 8 clean room | |
Clinical trial API manufacturing | Multi-line facility capable of a variety of reactions (Hirono plant) | ||
1,500L (GL/SUS) |
GMP |
1200L(SUS) low-pressure hydrogenation reactor (0.5MPa) 1,000 L (HC) super low-temperature reactor (-90℃) 2,000 L fluoride resin lined reactor ISO class 8 clean room |
|
API manufacturing | Capable of small-scale manufacturing (Hirono plant) | ||
100~600L (GL/SUS) |
GMP |
Column purifying device ISO class 8 clean room |
|
API manufacturing(1st plant) | 20 years of experience manufacturing APIs (Hirono plant) | ||
2,500~4,000L (GL/SUS) |
GMP |
Various mills (Counter jet mill, hammer mill and power mill) ISO class 8 clean room |
|
Intermediate manufacturing(2nd plant) | Cost reduction through large scale continuous production (Hirono plant) | ||
6,000~10,000L (GL/SUS) |
GMP |
6,000L(SUS) low-pressure hydrogenation reactor (0.4MPa) Handling n -BuLi |
|
Highly potent API manufacturing(3rd plant) | Category 5 high pharmacological active ingredient manufacturing facility (Hirono plant) | ||
600~800L (GL) | GMP |
Filter dryer (0.38m2) Spiral jet mill ISO class 8 clean room |
|
API manufacturing(4th plant) | Large multipurpose APIs production facility since 2017 (Hirono plant) | ||
2,000~10,000L (GL/SUS) |
GMP |
6,000L(SUS) low-temperature reactor (-30℃)L Counter jet millL ISO class 8 clean room |
Please contact us about cost/case/technology/quality control
Inquiry formIntroducing examples of custom synthesis
Customer case studies