FUJIFILM Wako ChemicalHirono plant
- LocationHirono-cho, Fukushima Prefecture
- Site area139,000 m2
- Number of employeesAbout 150
- Start of operation1990
- CertificationsISO9001 and ISO14001
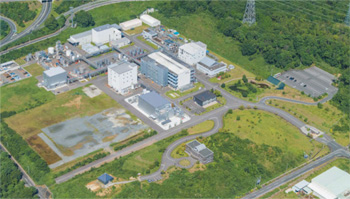
- Category 5 high pharmacological activity ingredient manufacturing facilities
- GMP compliant multipurpose facilities
- Equipped with a super-low temperature reactor, a hydrogenation reduction reactor, a fluoride-resistant oven which are GMP compliant , and various mills.
- Manufactures a wide range of pharmaceutical products incl. APIs, intermediates and high pharmacological activity ingredients.
- Acquired a drug manufacturing license in 1997 and an FDA license in 2016.
Main facilities
- Scale of the reactor:200 ~ 10,000L (GL, SUS, Teflon)
- Reaction vessel:GL reactor, SUS reactor, Hydrogenation reduction reactor(SUS: ~0.5Mpa), Teflon reactor, Super low-temperature reactor(~-100℃)
- Solid-liquid separation:Centrifuge filter, Filter dryer, High-speed decanter
- Drying facilities:Biconical dryer, Vibration dryer
- Special facilities:Dual-pipe concentrator, Multi-pipe concentrator, Various Granulation devices, Various mills
Manufacturing facility for highly potent APIs
- Category 5 (OEL:0.1μg/m3)
- 600L and 800L reactor
- Integrated manufacturing incl, micronization
Product | API & early phase drugs | cGMP non-sterile |
---|---|---|
Facilities |
Containment Area ・600 L(GL) Reactor x2 ・800L Glass Lined Reactor ・Filter Dryer(0.38m2)×1 Material: Hastelloy ®C22 equivalent ・Micronization equipment: Spiral jet mill General production area 600L(GL)x1 |
Multipurpose line ・Minimum mixing volume 50L ・Minimum mixing volume 50L ・Dryer filter capacity: 100L Micronization equipment ・Made by Food and Pharma Systems Analytical laboratory management system isolated from production facilities) |
Containment level | Category 5 | Down to OEL:0.1μg/m3 |
Cleanliness level | ISO class 8 c lean room (Class 100,000 equivalent) | |
Temperature range | ‒15~100 ℃ | Reactor Jacket media: Brine |
Building dimension | ≒900m2 Approx. 900m2 2 fl oor s teel ACL concrete |
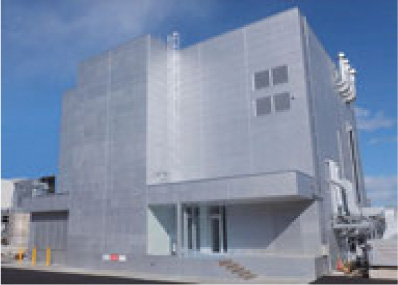
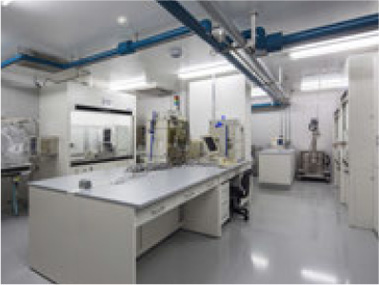
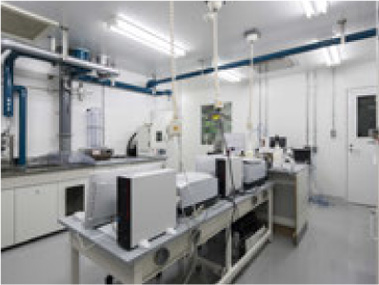
Large multipurpose API production facility
Ability to handle l arge scale production of API and intermediates
- 10,000L l arge capacity reactor
- API micronization capability (counter jet mill)
- Crystallization reactor
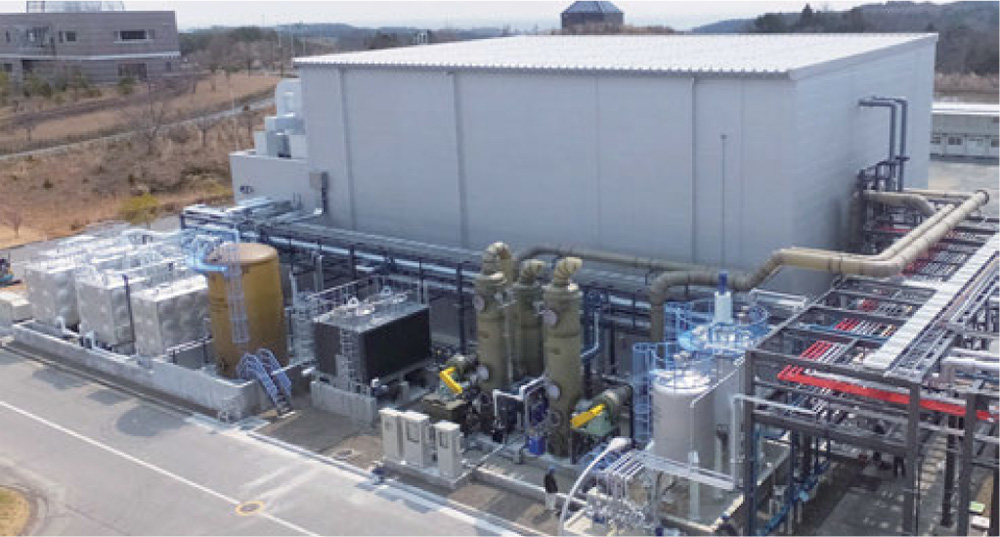
Scale | 2,000~10,000L(GL/SUS) |
---|---|
QMS | GMP |
Special notes | 6,000 L (SUS) low-temperature reactor (-30℃) Counter jet mill ISO class 8 c lean room |
Clinical trial API manufacturing
Multi-line facility capable of a variety of reactions
Scale | 1,000~2,000L(GL/SUS) |
---|---|
QMS | GMP |
Special notes |
1,200 L ( SUS) low-pressure hydrogenation reactor (0.5 M Pa) 1,000 L (HC) super low-temperature reactor (-90℃) 2,000 L fl uoride resin lined reactor ISO class 8 c lean room |
API manufacturing
Capable of small-scale manufacturing
Scale | 100~600L(GL/SUS) |
---|---|
QMS | GMP |
Special notes |
Column purifying device ISO class 8 c lean room |
API manufacturing (1st Plant)
20 years of experience manufacturing APIs
Scale | 2,500~4,000L(GL/SUS) |
---|---|
QMS | GMP |
Special notes |
Final crystallization reactor: 2,500 L Counter jet mill, hammer mill, and power mill ISO class 8 clean room |
Intermediate manufacturing (2nd Plant)
Cost reduction through large scale continuous production
Scale | 6,000~10,000L(GL/SUS) |
---|---|
QMS | GMP |
Special notes |
6,000 L (SUS) low pressure hydrogenation reactor (0.4 M Pa) Handing n-BuLi |