フロー合成法を用いた化成品の製造受託サービス
「フロー合成法」とは
フロー合成法とは、直径数百ミクロン~数ミリメートル程度の極細な管に、原料である化学物質を連続的に供給して混合・反応させる化学合成法です。
大きな反応釜で大量の原料を一度に混合・反応させる「バッチ合成法」と比べて、「フロー合成法」は生産量にあわせて一定の原料を連続的に投入するため、多品種少量生産ニーズへの対応が可能です。さらに、極細な管の中で反応条件を精緻に制御できるため、より高純度な化成品を生産することができます。
フロー合成法
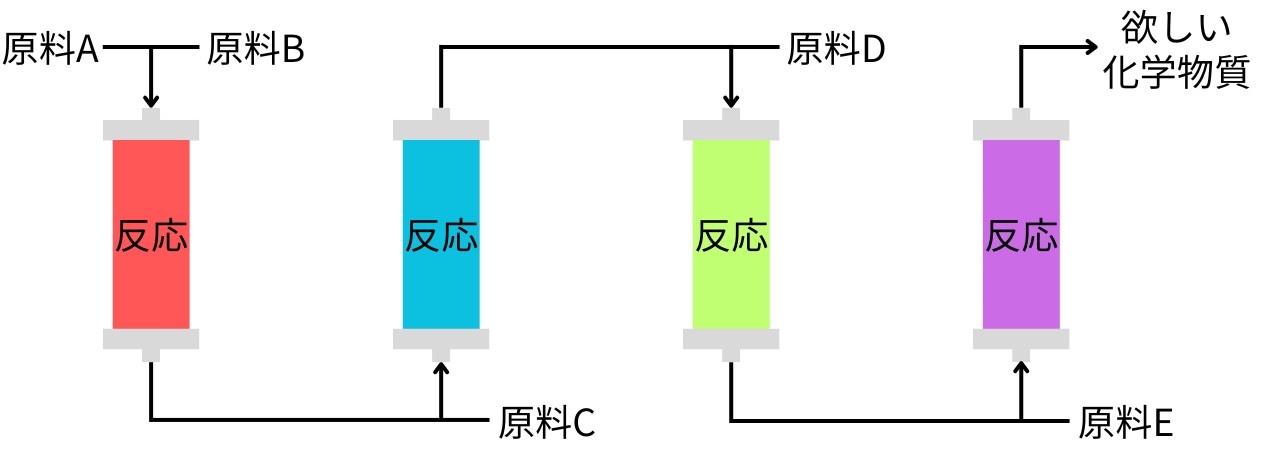
バッチ合成法
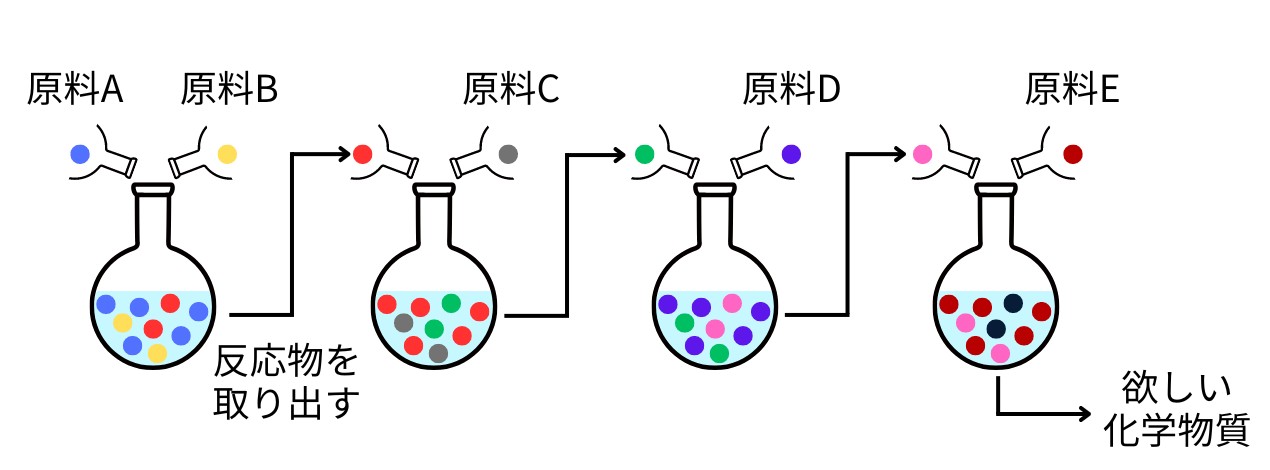
フロー合成法のメリット
フロー合成法を用いることで得られるメリットには様々なものがあります。ここでは、フロー合成法で得られるメリットの内、「環境への負荷低減」「生産量変動へのフレキシブル対応」「安全性の向上」についてご紹介します。
1. 環境への負荷低減
フロー合成法はバッチ合成法と比べて、「廃棄物量の抑制」「加熱冷却の負荷低減」「溶剤量の削減」などの観点から、環境への負荷低減に貢献します。
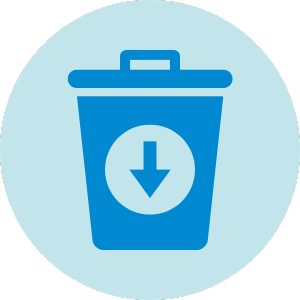
廃棄物量の抑制
フロー合成法は、高収率による不純物低減が可能なことから、廃棄物量を抑制することができます。
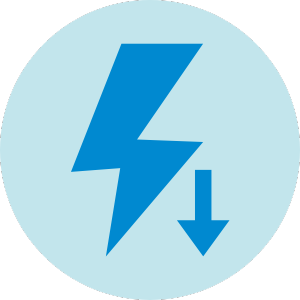
加熱冷却の負荷低減
フロー合成法では、小さな反応部だけを加熱冷却するだけで済みます。そのため、加熱冷却のエネルギーを削減することができます。
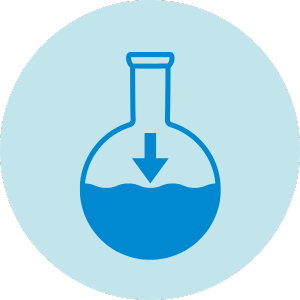
溶剤量の削減
フロー合成法は加熱冷却の効率が良く、高濃度で反応できるため、溶剤量を削減できる可能性があります。
フロー合成法とバッチ合成法のCO2排出量の比較
当社は、リチオ化およびホウ酸エステル化の低温逐次反応による化成品1kgあたりの生産において、フロー合成法はバッチ合成法と比べて、原材料の投入量と廃棄物量を抑制できることを確認しました。また、冷却に必要なエネルギー量を低減できることから、CO2排出量を約53%削減できることを確認しました。
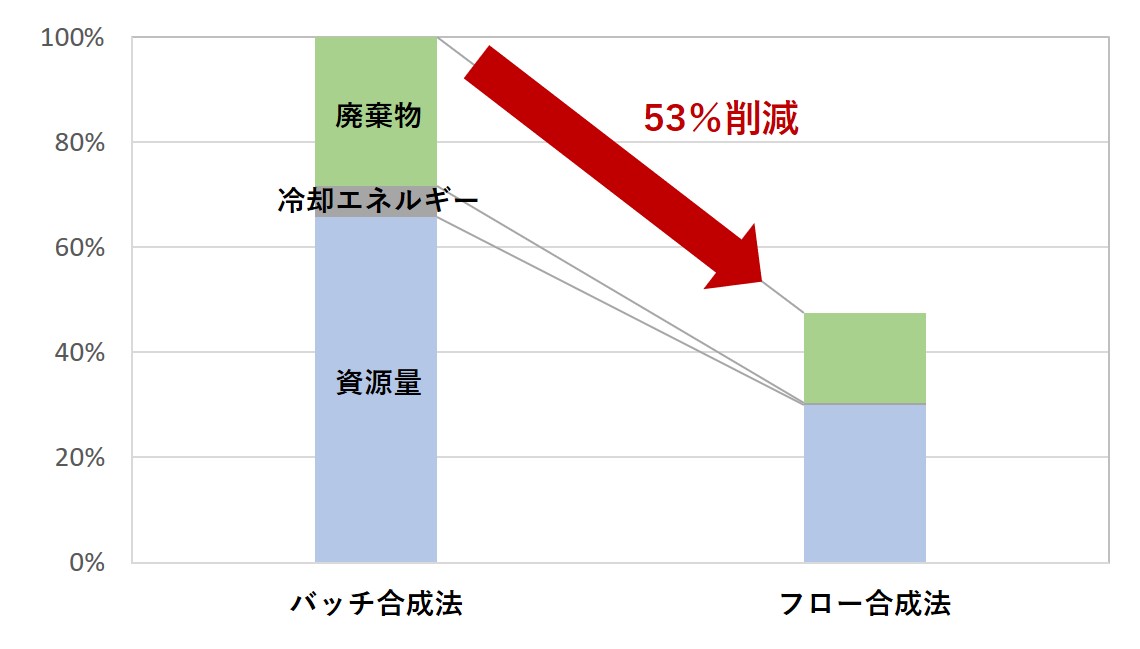
2. 生産量変動へのフレキシブル対応
バッチ法では、スケールアップの際に反応器をより大きなものへと変更する必要があります。 そのため、環境変化に伴う反応条件の調整が必要です。一方でフロー合成法の場合、反応液を連続的に流し続けることで生産量を容易に増やすことが可能です。
3. 安全性の向上
危険性の高い物質を用いる場合、一度に大量の化合物を使用するバッチ法と比べて、少量を連続的に流すフロー合成は遥かに安全です。 また、不安定な反応を行う場合にも、反応で得られた生成物が次の反応へと連続して使用されるため、ロスなく安全な合成が可能です。 フロー合成の反応空間は小さいため、万が一事故があった際にも被害を抑えることができます。
富士フイルム和光純薬のフロー合成法の特徴
1. 充実した開発と製造体制
富士フイルム和光純薬は、大量生産における製造実績とノウハウを蓄積してきました。 キログラムからトンスケールまで、お客様のニーズに応えていきます。
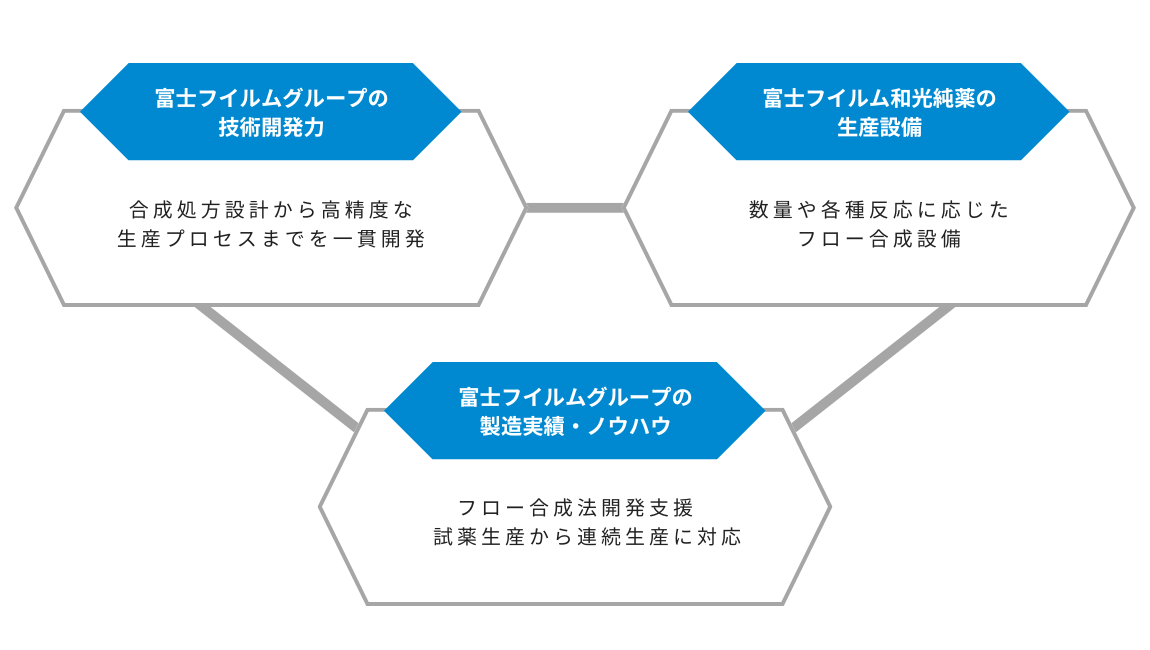
2. 最適な反応プロセスの開発
「温度シミュレーション」や「ベイズ最適化を用いた条件探索」によって、反応プロセスの設計を早く、確実に行います。 また、フロー技術とバッチ技術を融合することで、お客様にとって最適なソリューションを提供していきます。
温度シミュレーション
バッチ合成法では不可能な2段階温度制御プロセスを実現できます。
一般的に、2段階温度制御プロセスを用いるとパラメーターが増えるため、最適解の探索により多くの検討時間を要します。
ですが、当社はシミュレーションを用いることで、不純物の少ない高品質な領域へ迅速に到達することができます。
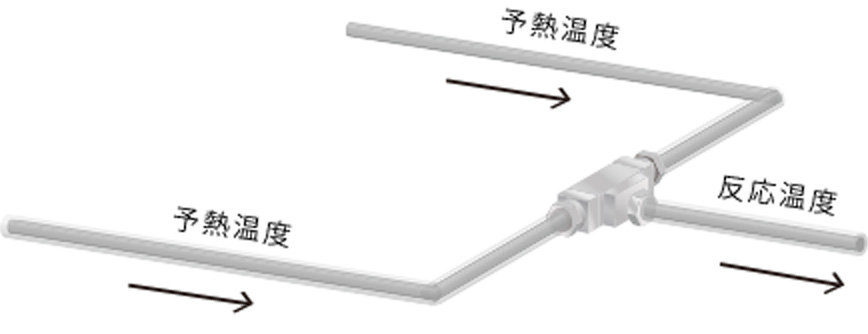
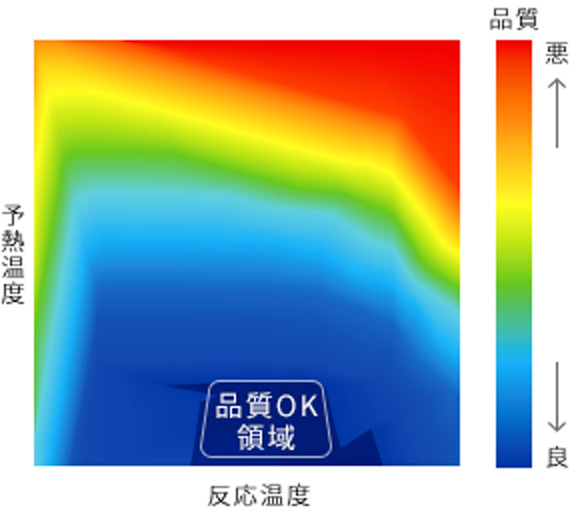
ベイズ最適化を用いた条件探索
ベイズ最適化とは、AIモデルが次の実験条件を自動的に提案してくれる手法のことです。 人の手で条件探索をする場合、組み合わせの膨大さや人間特有の思考の偏りによって、 最適な条件を見つけるまでに長時間を要したり、最適な条件が見つからない可能性があります。 しかし、AIによる偏見や先入観のない探索と処理能力を活用することで、より短い期間で最適な条件を見つけることができます。 実際、AIを用いた条件探索によって検討期間を約1/3に短縮した事例もございます。